Discover Aluminium
Aluminium is an exceptional, modern metal which continues to displace more traditional materials across many industrial sectors. This is due to both its attractive pricing level but also its exceptional combination of characteristics.
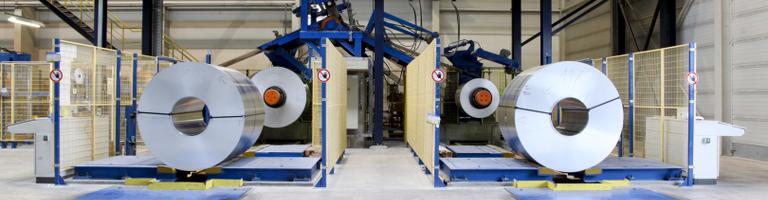
Transformability
Physically, chemically and mechanically aluminium is a metal like steel, brass, copper, zinc, lead or titanium. It can be melted, cast, formed and machined much like these metals. Often the same equipment and fabrication methods are used as for steel.
Price
Aluminium is the only metal, which can compete with steel on price. It is substantially cheaper than all other metals.
Light Weight
Aluminium is a very light metal with a specific weight of 2.7 g/cm3, about a third that of steel. Its strength can be adapted to the application required by modifying the composition of its alloys.
Recyclability
Aluminium is 100% and repeatedly recyclable with no downgrading of its qualities. The re-melting of aluminium requires little energy: only about 5% of the energy required to produce primary aluminium.
Aspect
Aluminium has a unique, modern, natural metallic aspect which is often used to promote the design and modernity of a products such as laptops, tablets and mobile phones.
Corrosion Resistance
Aluminium naturally generates a protective oxide coating and is highly corrosion resistant. Different types of surface treatment such as anodising, painting or lacquering are used to further improve this property.
Electrical and Thermal Conductivity
Aluminium is an excellent heat and electricity conductor and in relation to its weight is almost twice as good a conductor as copper. This has made aluminium the most commonly used material in major power transmission lines.
Reflectivity
Aluminium is a good reflector of visible light as well as heat, and that together with its low weight, makes it an ideal material for reflectors in, for example, light fittings or rescue blankets.
Flammability
Aluminium does not burn which explains why it is easy to recycle because it is simply re-melted. For this reason, it is widely used in building, transport, home appliances and offshore structures.
Aluminium – typically in coil form - is quite often combined with composite materials to make aluminium composite panels. The fire resistance of composite panels will depend entirely on the quality of the core material.
Ductility
Aluminium is ductile and has a low melting point and density. In a molten condition it can be processed in a number of ways. Its ductility allows products of aluminium to be basically formed close to the end of the product’s design.
Impermeable and Odourless
Aluminium is impermeable and odourless and, for this reason, widely used in alimentary and medical packaging.
Discover Anodising
What is anodising?
Anodising is an electro-chemical treatment which is specific to aluminium.
It is a controlled oxidisation or transformation of the surface of the metal which leaves a hard, transparent surface on the metal. Unlike paint or coatings, anodising is not a layer on top of the metal, it is an integral part of the metal surface.
The thickness of the anodic layer can be regulated as part of the anodising process. Typically, the range is from <1 micron (for purely technical applications) to 25 microns (for exterior building panel protection).
Anodising is ideally suited to maritime environments.
The market
The building and construction market is the largest market for aluminium in the world because of its unique combination of strength, lightweight, recyclability transformability and corrosion resistance.
Part of this market is the flat rolled products or sheet market used in building facades, ceilings, walls, composite panels etc.
If aluminium is not surface treated, the surface aspect will be irreversibly changed into a inconsistent, milky finish. Where the material is visible or will be an architectural feature, it must either be coated or anodised.
Colouring
The anodic film layer can be coloured through three processes. All three colouring processes retain the genuine metallic sheen of the metal.
- Electrolytic colouring where metallic salts are integrated into the anodic film layer. With this type of colouring, the colour is achieved optically. It will not fade even with exposure to sunlight over many years. Using this process, finishes similar to bronze and copper can be achieved.
- Auto-colouration is where the colour is achieved through natural anodising of certain specific aluminium alloys. Typically, this will give grey colours similar to zinc
- Organic dye colouring where dyes are introduced in the anodic layer as part of the anodising process. A wide range of colours is available although – like other organic finishes such as paint – these colours will fade over time, particularly if used outside. The fading varies according to each colour. Sometimes organic dyes may be combined with electrolytic colours so that the fading is less visible.
The anodising process
Batch anodising
Typically, metal in its various forms (extrusions, sheets or panels) are introduced vertically on racks in a series of vertical treatment cells. This is known as Batch Anodising. There are many batch anodising plants throughout the world. Batch anodising produces a very hard anodic layer which typically does not permit transformation (such as bending) after the anodising process.
Over time, the anodic layer from batch anodising will suffer from erosion with a reduction in the level of protection. In addition, because of the lack of precision in the batch anodising process, large surface areas (such as sheets) often suffer from lack of surface uniformity. Batch anodising plants typically lack the economies of scale to install the continuous renewal of certain treatment baths which is fundamental to a quality anodised surface.
Aloxide continuous anodising
In 1972, we perfected a hybrid anodic film layer which was flexible and could permit anodising to be carried out on a continuous horizontal basis through horizontal treatment cells whilst still in coil form.
The superior process control of the continuous anodising process meant that surface uniformity was much improved over the batch process.
Anodising in coil form meant that the production process could be highly automated resulting in lower costs and further contributing to consistently of the surface finish.
This new form of anodising also permitted the treatment of pre-fabricated coils (e.g. pre-perforation)
In addition, the flexible film permitted the metal to be transformed (e.g. by bending) after anodising
In time, a further benefit was discovered. Unlike the batch anodised product, the continuous anodising film did not suffer any surface erosion when employed in long term outdoor exposure.
Aloxide Vertical Anodising
In 2018, we introduced a new vertical anodising process on to the market.
This is a next generation batch anodising process which creates the same flexible anodic film on the surface of the metal as with continuous anodising with two particular characteristics:
- The production is highly automated, and
- The process control is similar to that in the continuous anodising process
The result is a high quality, consistent surface finish identical to that achieved in the continuous process.
So for the first time, Aloxide became available in less than full coil quantities across a major part of its product range. We were also able to extend our product offering to profiles and sections.
Authentic anodising technology
We only produce pure high quality anodised aluminium in a very wide dimensional range and with the possibility of high anodic film layers for external exposure.
Many companies have tried to introduce products on the market which seek to emulate the pure anodised product through the use of transparent coatings. These coatings - because they are not an integral part of the metal surface - can never substitute the protection afforded by an authentic anodic film layer.
Anodising as a substitution for other materials
When combined with UV-proof colouring technology, anodised aluminium is a perfect substitute for other metals, achieving a similar aspect and mechanical properties but at a lower (often much lower) price, including:
- Stainless steel
- Copper
- Brass
- Zinc
- Titanium
Other surface finishes on aluminium
Coating – most commonly painting – on aluminium has been aggressively developed by paint manufacturers and coil coaters over recent years.
The advantage over anodizing is that coated finishes are available in a very wide range of colours and finishes. However, the vast majority of painted aluminium is mainly produced in white, black, silver and grey.
The on-site performance has been far from successful:
- As an organic coloured coating, it is guaranteed to fade over time
- ‘Metallic’ finishes – used to copy a true metallic finish – never look or feel truly metallic and quickly lose their sparkle to leave a flat matte finish
- As a coating, paint is fragile and can be easily scratched and damaged
- Damaged paint will lead to surface corrosion and ultimately failure
- The paint finish is subject to chalking
- As a coating, paint will over time lose its adherence and peel off the surface
Performance is particularly weak where the material is exposed to high levels of heat, humidity and pollution found in many large Asian cities.
The lack of integrity of painted aluminium can be seen in the guarantees which are lengthy and full of exclusions.
Applications for Aloxide
Architectural
The construction market is the world’s largest end-market for aluminium. Aloxide is an added-value product which can be can be used for:
- All types of solid panel building façade applications
- Interior solid panel walls and ceilings
- Composite, honeycomb and insulated panels
- Rain screens
- Standing seam roofs
- Guttering
- Soffits and facia panels
- Laminated door panels
- Interior decorative elements
- Complex structures such as perforated panels or expanded mesh
Public Works
Highway sound barriers are increasingly used to protect from sound pollution in cities worldwide. Unfortunately, sound barriers also provide a perfect canvas for graffiti artists. Aloxide provides a durable decorative finish permitting the easy removal of graffiti.
Welded tubes
Aluminium welded tubes are light but strong. They are used in a whole range of applications from domestic to industrial.
Automotive
The automotive industry has been one of the most recent converts to aluminium for reasons of weight reduction and recyclability. Applications for Aloxide include:
- Exterior/interior automotive trim
- Technical applications
Consumer goods
As demonstrated by manufacturers of laptops, mobile phones and tablets, anodised aluminium has become the symbol of clean, modern lightweight design with the added advantage of 100% recyclability at the end of its design life.
Aloxide can be used extensively, including for:
- Designer furniture
- Luxury luggage
- Kitchens
- DIY applications
- Electronic goods
- White goods
- Decorative applications
- Letterboxes
Medical
Aloxide can be used in equipment employed in hospitals and clinics because of its very smooth easy-to-clean finish which reduces the risk of accumulating germs which might otherwise lead to infection.
Aerospace
Aloxide can be used in a variety of on-board applications such as aircraft trollies and catering boxes. It is lightweight and resistant to high wear and tear.
Signage
Aloxide can be used in signage application providing greater resistance than paint and an authentic metallic design finish.
Processing Methods
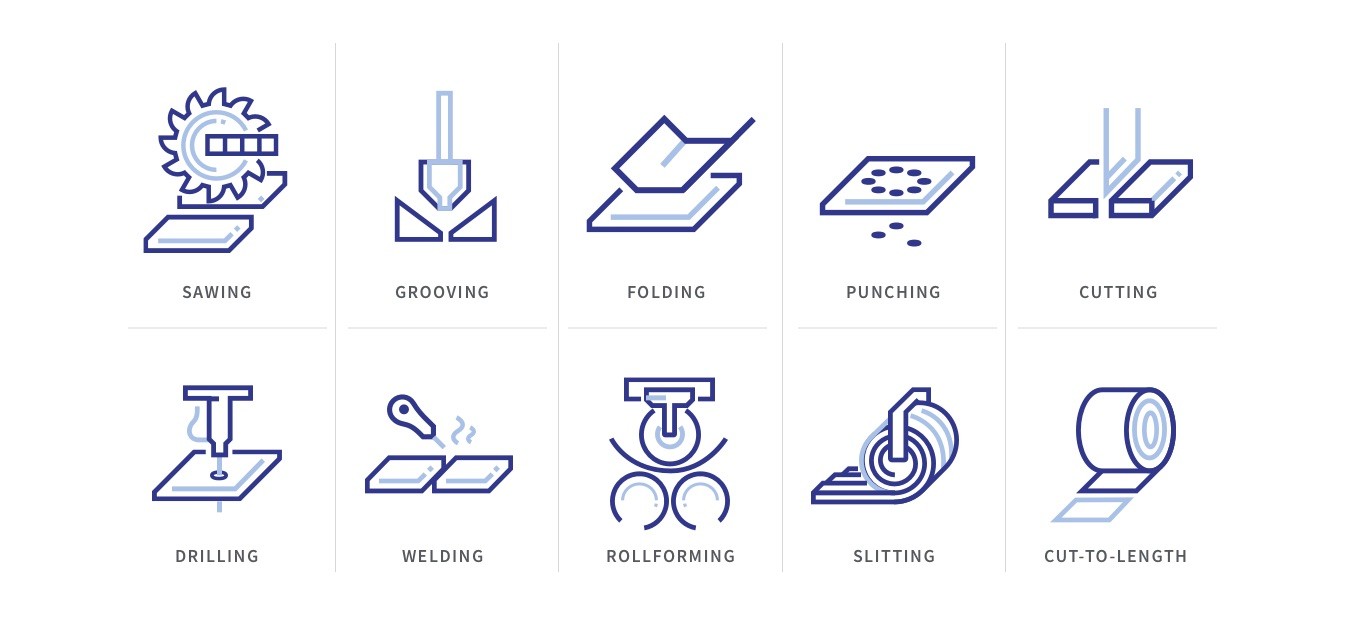